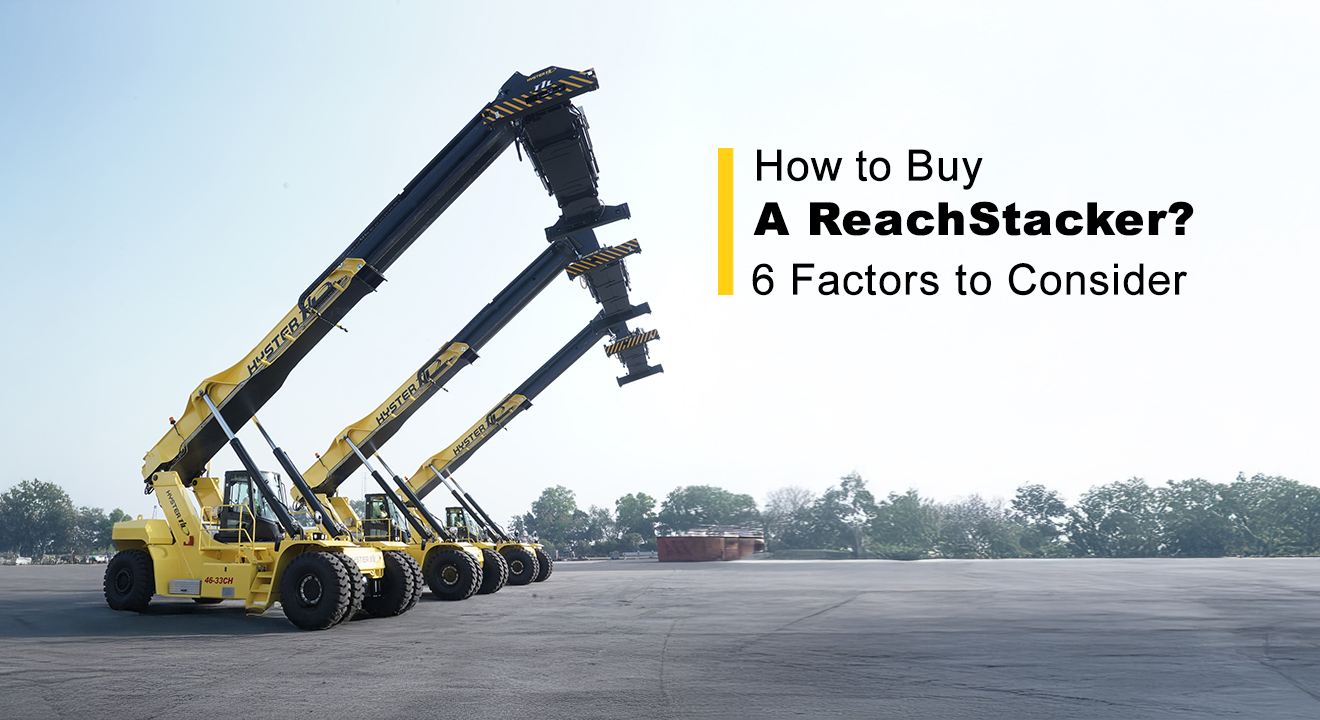
When comparing reachstackers, the specifications listed on paper are only the first step. If you are an engineer or an operator, then you must consider more than just lifting capacity. When purchasing these powerful machines, try to understand how they operate in real-world settings.
There are a number of factors that can affect operational efficiency, such as the hydraulics, load stability, and third-row reach. Along with these, you must also focus on the drivetrain and sensor integration.
So, when selecting the best container handling equipment, this guide will help you make the right investment.
1. Lifting Capacity vs. Reach Distance
The performance of 45-ton reachstackers varies from row to row. If you refer to the load charts, the same machine may lift only 27 tons in the second row and only 16 tons in the third. Now, this becomes crucial if the arrangement of your yard necessitates regular third-row stacking.
In this respect, the Hyter-TIL Reachstacker has a leverage - lifting 46 tons at close range (first row), 33 tons at the second row and 17 tons at extended reach (3rd container row). This additional load-handling capability ensures faster container turnaround, reduced downtime, and enhanced operational efficiency.
Moreover, the ReachStacker wheelbase length directly affects stability and lifting force. Normally, the wheelbase length is between 6 and 9+ meters. Thus, engineers also need to take this factor into account to ensure safe and effective operations.
2. Drivetrain Components: Engine, Gearbox, and Axle
The performance and uptime of a reachstacker make it ideal for port logistics. These features are directly impacted by the engine, transmission, and front axle. The versatile ReachStacker from Hyster TIL has a solid reputation for long-term dependability and high torque, with sturdy front axles and tested gearboxes.
While specifications are important, they shouldn’t be the only factor in your container handling equipment purchase decision. You can also verify local service support and part availability. Selecting a model with access to OEM support is essential to prevent downtime.
3. Boom Design & Hydraulic System
The boom is more than just metal—its strength comes down to steel grade, weld integrity, and structural reinforcements. The reliability of the telescopic mechanism is also necessary, as any weak points can lead to costly failures.
Hydraulic performance is equally critical. Smooth, precise lifting depends on proper oil flow rates, pressure stability, and the quality of control valves. Modern reachstackers now use load-sensing hydraulics that adjust flow based on the actual load, improving both fuel efficiency and operator control.
Alongside this, don’t overlook cooling, especially in the Indian climate, to maintain consistent performance. Pay attention to the design, as the hydraulic systems rely on heat exchangers and thermostats to prevent overheating. You can also download spec sheet to have a look at the technical details.
4. Anti-Tipping Technology & Sensor Integration
To lower operator danger and avoid mishaps during large lifts, modern port logistics machinery has seat switches and dynamic anti-tipping technology. You can also find load-sensing controls and twist-lock detection in the ReachStacker, which ensures machine and operator safety. Watch what an operator has to say about the Hyster-TIL ReachStacker, which is best for tight yard operations.
During prolonged or high-reach operations, stability control in these machines is particularly crucial for preserving equilibrium. Simultaneously, ergonomics and tools for the operator are also important. You can also look for features like wide-angle cab visibility, operator presence sensors, and simple joystick controls.
For 360° situational awareness, sophisticated devices include cameras, radar, and smart sensors. For example, the Hyster-TIL ReachStacker comes equipped with a motion cut-off system, a cabin proximity sensor, LMI display and a spreader rotation cut-off for enhanced safety and control.
5. Fuel Types and Emissions
Even though diesel reachstackers are still being utilised, hybrid and electric variants are becoming more popular because of their quieter operation and reduced emissions. Engines that run on alternative fuels, such as hydrotreated vegetable oil (HVO), can cut CO2 emissions by up to 90% without compromising performance for operators who are concerned about sustainability.
Additionally, software efficiency is increasing. Depending on the workload and circumstances, features like Eco-drive modes, automated stop/start, and intelligent power management can result in fuel savings. So, while assessing different port logistics machinery models, examine how these modes are included in the operator interface.
6. Maintenance Accessibility
Accessibility is crucial when it comes to reachstacker maintenance. So, look for equipment which are strategically positioned. Wiring, hydraulic filters, oil filters, and diagnostic ports should all be accessible without requiring the removal of important parts. You can examine the unit in person if at all possible. Over time, features like integrated service panels and gas-assisted hood lifts can drastically reduce maintenance expenses and downtime.
Choosing the Right Reachstacker for Real-World Performance
Choosing the best reachstacker needs a thorough technical analysis rather than just reviewing the specifications. In addition to confirming the factors mentioned above, an engineer or operator should examine load charts at all reach depths.
Environmental and operational objectives should be in line with fuel type and emission compliance. Additionally, don't ignore serviceability as quick access to components, diagnostics, and filters can reduce downtime and overall cost of ownership.
If you are looking for more information on heavy lifting vehicles, keep following our blog page. With this comprehensive examination guide, you can confidently choose machines that provide dependable, effective, and safe performance. Alongside, you can also explore 6 powerful cranes used in modern construction.
FAQs
What is the cost of a reach stacker?
The cost of a ReachStacker can vary widely depending on factors like lifting capacity, brand, and fuel type (diesel, hybrid, or electric). The price also differs based on the inclusion of advanced features like Eco-drive systems, automated stop/start, and telematics. New models will typically fall at the higher end of the market. For the most accurate pricing, it's best to request a quote based on your specific operational needs and site conditions.
How much can a Hyster-TIL ReachStacker lift?
A Hyster‑TIL (Hyster RS46 series) ReachStacker offers impressive lifting capabilities tailored for heavy container handling. The first row (closest to the operator/ground) is up to 46,000 kg. The second row (one container in) is around 33,000 kg, and the third row (two containers deep) is approximately 17,000 kg.
Is ReachStacker the same as a forklift?
No, a Reach Stacker is not the same as a forklift, although both are used for material handling. The key difference lies in their design and function. ReachStackers are specifically built to handle shipping containers, often in ports, rail yards, or container depots, while Forklifts, on the other hand, are more commonly used in warehouses or industrial settings.
What should you choose - diesel, hybrid, or electric ReachStacker?
Diesel reachstackers remain popular for heavy-duty, high-frequency workloads and lower upfront investment. Hybrids bridge the gap by offering decent fuel efficiency and power, while electric models are ideal for terminals or warehouses prioritising zero emissions and noise reduction. Your decision should revolve around your lifting needs.